Technology news
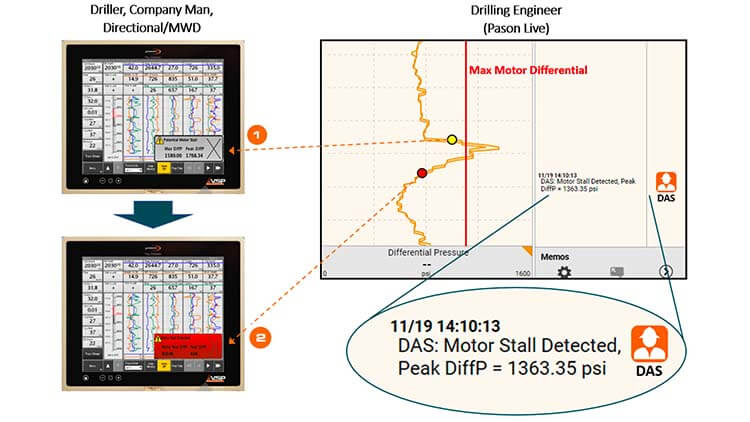
Drilling intelligence
DAS Motor Stall Detection (EDR 19.7)
January 31, 2020
DAS Motor Stall Detection (EDR 19.7)
PDF: Published on Pason, January 31, 2020
DAS automatically detects and alerts when there is a motor stall. A memo with additional information is generated for historical reference, and to monitor frequency of stalls. This information can be used to modify drilling parameters, to prolong motor life, and potentially save a costly trip.
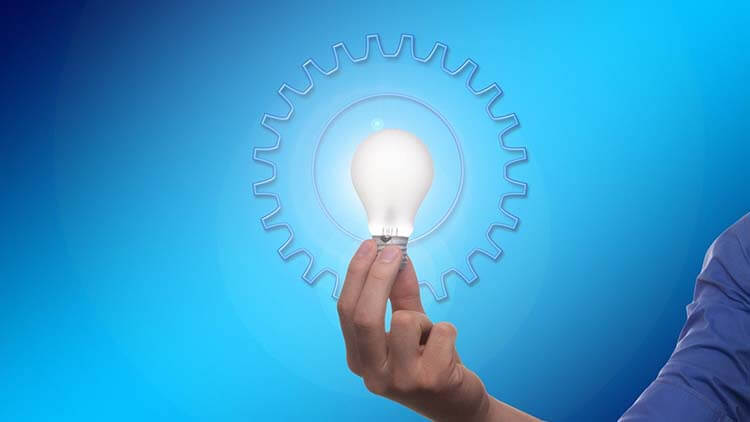
Drilling intelligence
Method, System, and Medium for Controlling Rate of Pentration of a Drill Bit
PATENT: Published on Canadian Intellectual Property Office, November 12, 2019
Credits
Holt, Trevor Leigh (Canada)
Wilson, Thomas William Charles (Canada)
Hepburn, Quinn Harrison (Canada)
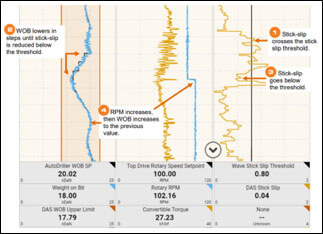
Technology
Stick Slip: a costly torsional vibration
July 11, 2019
Stick Slip: a costly torsional vibration
STORY: Published on Pason Systems, July 11, 2019
While drilling a well in today’s fast paced oil and gas business, drilling operations can experience many downhole vibrations that lead to costly drilling inefficiencies. One such phenomenon is stick slip – a form of torsional vibration that occurs when the bit, bottom hole assembly (BHA) and/or drill string experience different rotational speeds than expected.
Credits
Matthew Huber
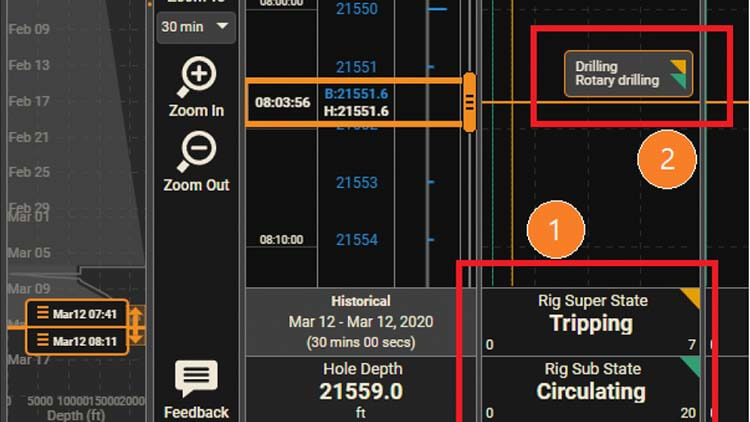
Drilling Data
Rig State Traces (EDR 19.4 and higher)
April 15, 2019
Rig State Traces (EDR 19.4 and higher)
PDF: Published on Pason, April 15, 2019
The EDR includes two traces you can use to determine the rig's state at a specific time or depth: Rig Super State and Rig Sub State. The super state describes activity at a high level, while the sub state provides more detail.
These traces are available on the EDR, DataHub, and Pason Live in full 1-second frequency.
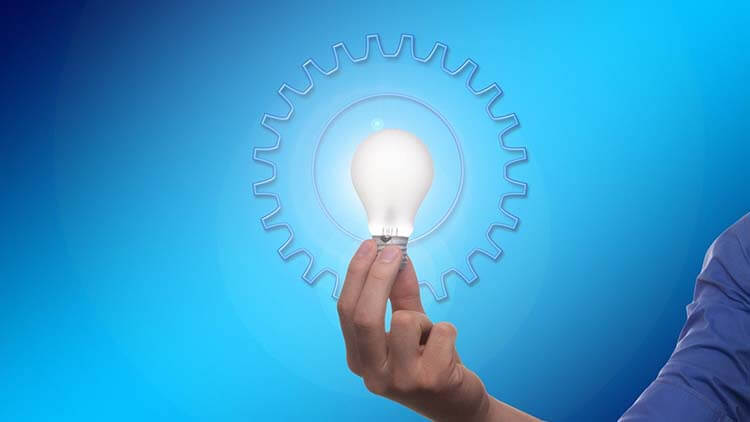
Drilling intelligence
Method and apparatus for drilling a new well using historic drilling data
PATENT: Published on United States Patent, March 19, 2019
A method for drilling a new oil or gas well in a selected geographical location includes extracting drilling modes from historic drilling data obtained from a group of drilled wells in the selected geographical location using a pattern recognition model. Each drilling mode represents a distinct pattern that quantifies at least two drilling variables at a specified drilling depth. The method also includes selecting a sequence of drilling modes at positions along a reference well as reference drilling modes that represent more efficient values for a selection of one or more of the at least two drilling variables compared to other extracted drilling modes; associating drilling parameter settings with the reference drilling modes; and drilling the new oil or gas well applying at least some of the drilling parameter settings.
Credits
Kristjansson; Sean (Calgary, CA),
Lai; Stephen (Calgary, CA)
Tremaine; Dean (Calgary, CA)
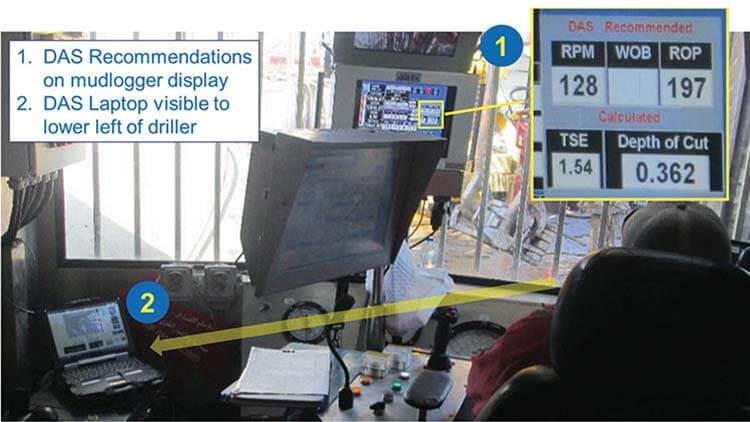
Drilling intelligence
Real-Time Advisory System Mitigates Drilling Vibrations in a Lateral Section
ARTICLE: Published on Journal of Petroleum Technology, September 1, 2018
A real-time drilling-data analysis and recommendation system that leverages surface drilling data was deployed in a lateral section of a well from an artificial island in Abu Dhabi. A key objective of this technology was to provide the driller with an easy-to-use display of a novel drilling-performance map. This paper presents data from the demonstration run, illustrates the features of this technology, and provides general observations on optimization of drilling parameters in this hole section.
Background
A research prototype drilling advisory system (DAS) was set up on an island rig with a wellsite information transfer specification (WITS) data feed from the mudlogger cabin over a fiber-to-serial cable to the computer in the driller’s cabin.
The DAS helps the driller make decisions for managing controllable drilling parameters to enable a high rate of penetration (ROP) and low vibrations. The system uses surface data only (i.e., data obtained from sensors instrumented on surface equipment) from the mud logger. The platform then analyzes the data and displays basic surveillance information, including heat maps that vary with the controllable drilling parameters. On the basis of this data and processing algorithms, the system makes recommendations for the controllable parameter values.
Data from three intervals were analyzed, and two of the three saw contrasting trends of stick/slip [torsional severity estimate (TSE)] and mechanical specific energy (MSE) with increasing rotary speed, whereas one interval did not see such a trade-off. The complex interplay between these dysfunctions requires an application-specific real-time advisory system to provide optimal drilling performance.
The control variables for this drilling application were ROP and rotary speed.
Credits
This article, written by Special Publications Editor Adam Wilson, contains highlights of paper SPE 188942, “Mitigating Drilling Vibrations in a Lateral Section Using a Real-Time Advisory System,” by J.R. Bailey, SPE, and G.S. Payette, SPE, ExxonMobil; M.T. Prim, J. Molster, and A.W. Al Mheiri, Zakum Development; P.G. McCormack, SPE, Halliburton; and K. LeRoy, Pason Systems, prepared for the 2017 Abu Dhabi International Petroleum Exhibition and Conference, Abu Dhabi, 13–16 November. The paper has not been peer reviewed.
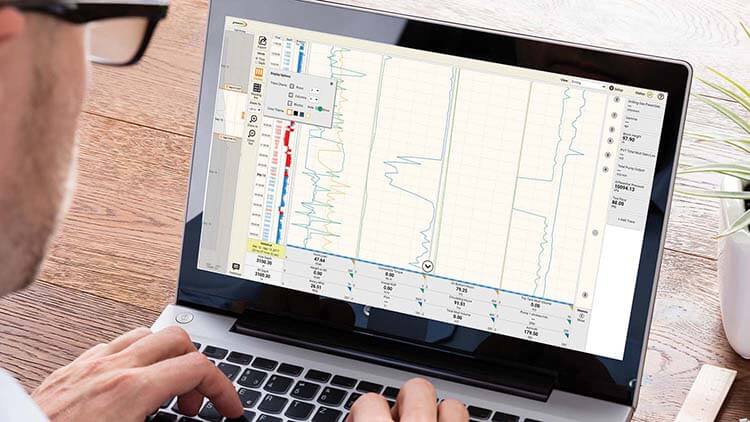
Technology
Pason Live launches in all business units
June 15, 2018
Pason Live launches in all business units
STORY: Published June 15, 2018
Pason's newest data viewer, Pason Live, was officially launched in all business units this spring.
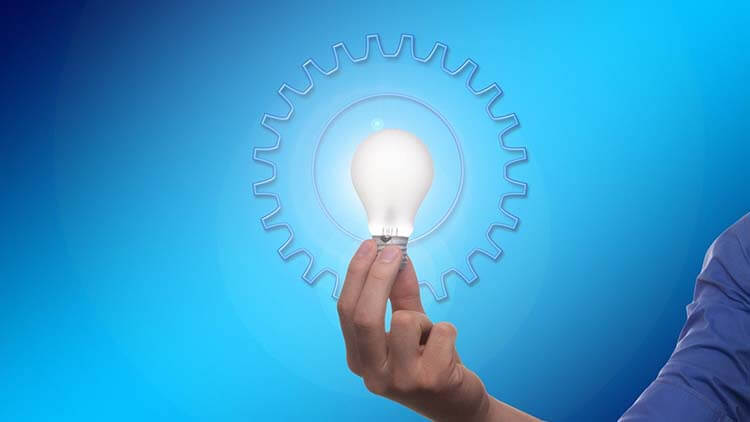
Drilling intelligence
Method and System for Performing Automated Drilling of a Wellbore (CA)
PATENT: Published on Canadian Intellectual Property Office, June 5, 2018
Methods, systems, and techniques for performing automated drilling of a wellbore. The wellbore is drilled in response to a first drilling parameter target (such as weight on bit) that includes a first drilling parameter offset modified by a first drilling parameter perturbation signal. A first drilling performance metric (such as rate of penetration) is measured and is indicative of a response of the drilling to the first drilling parameter target. An output of a first objective function is determined using the measured first drilling performance metric. A first correlation between the output of the first objective function and the first drilling parameter perturbation signal, and an integral of the first correlation, are determined. The first drilling parameter target is updated using the integral modified by the first drilling parameter perturbation signal. The wellbore is drilled in response to the updated first drilling parameter target.
Credits
Ng, Choon-sun James (Canada)
Khromov, Sergey (Canada)